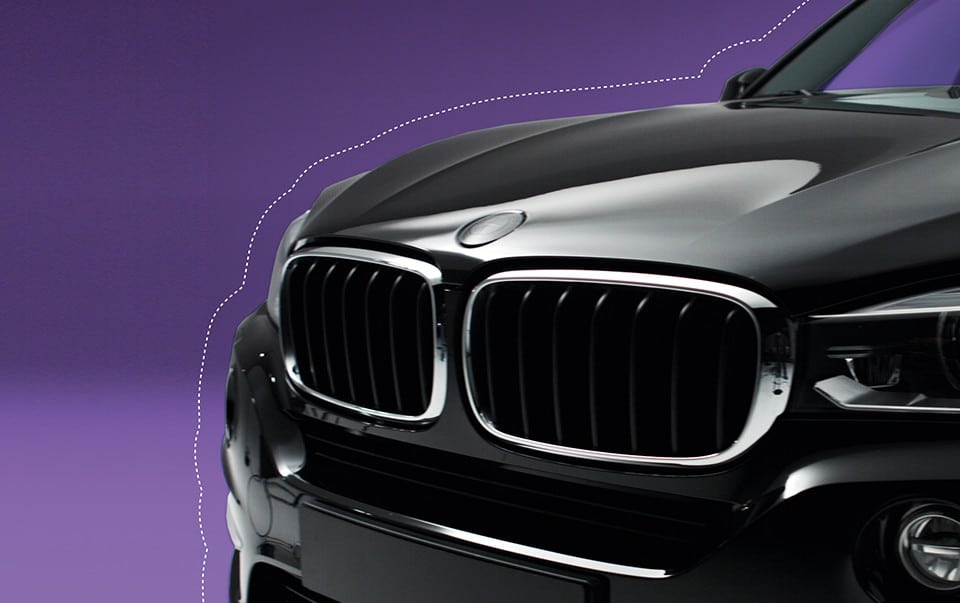
What is a Paint Protection Wrap? Here’s 1 Awesome Example
Awesome Paint Protection Video
Paint protection film (PPF, also called clear bra, clear film or clear paint film) is a thermoplastic urethane often self healing film applied to painted surfaces of a new or used car in order to protect the paint from stone chips, bug splatters, and minor abrasions. This film is also used on airplanes, RVs, cell phones, electronics, screens, motorcycles and many other areas. Paint protection film is OEM approved by virtually all car manufacturers.
Paint protection film is installed on a limited basis by manufacturers on various pieces of cars at the factory (e.g. the rear arches of Porsches). This film is most commonly applied to high impact areas of vehicles. The film is generally installed by certified trained professionals who receive supplies from outside distributors and dealers.
Contents
Military origins of paint protection film
As with many other consumer products, paint protection films were first developed and used by the military. During the Vietnam War, helicopter rotor blades and other sensitive parts of military transports were often damaged by flying shrapnel and debris. In order to help protect these moving parts, the US military asked 3M to come up with a solution that was both inconspicuous and low-weight.
The advantage of replaceable film over the replacement and repair of damaged rotor blades was immediately clear and its adoption was uncharacteristically quick for the US military. As a result, there are still people in the industry who refer to PPF as “helicopter tape” although this term is becoming less and less common as automotive applications have taken precedence.[1]
Adoption of PPF by automotive sector
Paint protection films use by the military has continued to the present day and 3M now makes a wide variety of aerospace and military films.[2] With time, however, the automobile industry began to take note of the protective benefits of PPF and it was soon being employed by race car drivers despite the difficulty of working with the original films. According to Kathy Lam, marketing manager for the automotive division of 3M “The first films were thicker and less compliant, [because] their purpose was to help keep helicopter blades from eroding in the harsh, sandy environments to which they were exposed. Because the blades were flatter and less complex than automotive surfaces, they didn’t demand a highly flexible, conformable film.” [3]
Contemporary automotive paint protection films
Today’s automotive PPF is highly conformable and optically clear and is available in a variety of thicknesses (measured in mil in the US) and colors. New products are multi layered and offer a self-healing top coat capable of reforming itself after being scuffed or scratched, maintaining clarity for more than ten years. Products from some vendors also offer hydrophobic properties, similar to those provided by a ceramic paint coating. Contemporary applications require a slip solution or gel as a barrier keeping the film from adhering to the painted panel. Custom and advanced applicators use steam, heat guns and torches to help apply film to complex surfaces. Pre-stretch and pre-form of films are also used for complex wraps and curves. Paint protection film has many different manufacturers/distributors present in the North American market.
Types of installation available
There are different styles of installation of PPF. Installation with a plotter can be done using software designed to create a pattern to the shape of the panel the film is being installed on. It is possible to modify a plotter software pattern to suit the needs of an installer and/or their customer. The most experienced installers can actually hand template panels, and then convert those templates into digital format for software to then cut them digitally, meaning that any custom work can be converted into a digital template. Installation without a plotter, by bulk installing film from the roll, is a risk, as the film is cut directly onto the surface of the vehicle.
In addition to installations performed in situ at the factory or by certified shops and dealerships, there are also a select number of vendors who sell pre-cut and vehicle specific paint protection kits, as well as individuals who sell these kits on online auction sites or other markets.
PPF is designed specifically for physical protection against light road debris and scratching on paintwork. It is different from sealants which are usually in liquid form and are designed for UV and chemical resistance. Sealants harden up the clear-coat on your paintwork, but are not designed to protect your vehicle from physical damage. For this reason, both PPF and sealants can be used on vehicles to protect the panels in different ways.
*******************************************************************
If you’re looking to add this great profit center to your shop, check out the all new MUTOH ValueCut vinyl cutters.
MUTOH America is he leader in vehicle wrap print and cut technology. MUTOH Makes It Possible.
Also check out Avery Paint Protection Film for the best install
SEE YOU AT SEMA!
Read More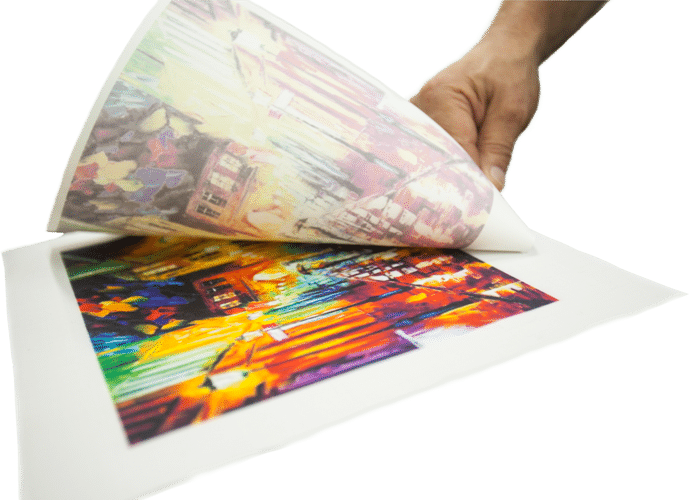
Choosing the Best Transfer Paper for Great Output from a MUTOH Printer
Choosing a transfer paper for your MUTOH printer for optimal output.
So, you’ve either bought a MUTOH dye sublimation printer or are looking at one. If you are now looking at transfer paper for a MUTOH printer there are some things you may want to consider.
Raw papers vary in particle size and particle distribution affecting its density and uniformity which in turn affect the absorption and adsorption of ink without any dot gain control while at the same time making the release of the dye uncontrollable as well. MUTOH printers are industrial designed printers designed with high resolution capability to output very high quality images for hard substrates while providing the speed capacity for high volume output, so uncoated papers are not recommended.
The secret sauce in dye sublimation transfer paper is the coating and there are primarily two basic types of coating.
High load or solid surface ‘clay’ coated papers have the most universal applications and can be used on the widest range of finished products. These work well for solid surfaces like metals, ceramics and glass as well as fabrics for soft signage, apparel, home décor and rubber koozies. Clay coated papers are high load papers, they can take high ink loads at print, but then dry fast. They are also gas permeable allowing excess sublimation gas to escape through the paper rather than creating blowouts or ghosting. While they don’t transfer as efficiently as CMC coated paper, they are friendlier to unstable print room environments making it a better choice first time and lower volume users.
High release or CMC (CarboxyMethyl Cellulose/ cellulose gum) coated papers work well for textile applications like fashion, apparel, home décor and soft signage. The high ink release property of these papers means it leaves less ink on the paper, requiring less ink to achieve the same color gamut, therefore reducing ink costs. The ‘high release’ property of these papers means this paper also releases that ink quicker, for less ghosting, shorted dwell times and higher productivity. While CMC papers are slower drying, they are still the choice for high speed printers.
Coatings plus.
Take a CMC coated paper and add a heat activated adhesive to it and you have Thermo Adhesive or ‘tacky’ paper. This allows the paper to ‘stick’ to the polyester fabric eliminating ghosting with slippery textiles and sports apparel. It eliminates difficulties when using clam shell presses that can shift during pressing causing blow outs or ghosting. It is a bit more expensive than other CMC coated papers and does not stick to hard substrates. It really shines when sublimating pre-sewn clothing, sticking to the garment allowing pressing of the second side while still attached leaving no lightening of the first side, giving a uniform two sided garment. https://www.thinkMUTOH.com/it-is-a-bit-tacky-but-for-me-it-really-is-all-over/?v=7516fd43adaa
Coatings plus, take two.
Take a coated paper and add a special UV inhibitor formulation and you have Kaspar Papir’s Sunpaper. The UV inhibitors in this paper actually gas with the dye sublimation dyes and encapsulate the dye around the layers of polyester fabric fibers, absorbing into the polyester with the dye molecules. So this is not a surface treatment and it needs no additional processing. Print and sublimate as normal to get extended outdoor protection typically double that of unprotected processes.
Special thanks to:
Rob Repasi – who provided the technical information.
Mark Freeman – President Digital Print Solutions, Inc. for providing the information on Kaspar Papir Sunpaper. http://www.kaspar-papir.com/
Need help choosing the right MUTOH wide format printer? Use the link below for assistance. we can walk you though a simple process to make sure you get what you are looking for.
http://www.thinkMUTOH.com/help-choosing-a-MUTOH-printer/
Read More